If you’re a manufacturer or wholesale distributor, you’re most likely looking to increase labor productivity, reduce handling time and optimize space utilization.
This can be a daunting task unless you have a tool in place that gives you a 360-degree view of your warehouse operations.
NetSuite’s Warehouse Management System (WMS) optimizes day-to-day warehouse operations using industry leading best practices — including intelligent pick and pack processes, handheld barcode scanning, cycle counting and integration with shipping systems — to run your warehouse more efficiently and minimize handling costs.
NetSuite WMS guides users through important tasks, from receiving and storing items to picking and shipping them, in the most efficient way. As items are processed in the warehouse, each transaction entered is automatically updated in NetSuite inventory and reported in real-time. NetSuite WMS provides a variety of key functionalities to better manage inventory and warehouse operations.
Let’s take a closer look at three key functionalities you can use to enhance your warehouse management.
1. Warehouse Set Up
The first key functionality is your warehouse set up. This is where you establish your warehouse layout in NetSuite. Once that’s complete, you’ll be able to set up and expand on the following features:
- Item alias/multiple UPCs: Set up multiple UPC codes for items
- Task management: Generate, prioritize and assign tasks to mobile users
- Cycle count plans: Create templates for your company’s most commonly generated cycle counts, run them on demand and assign them to mobile users
- EDI/ASN support: Generate ASNs and related EDI transactions automatically
- Unit of measurements: Transact in any unit of measurement (UOM) assigned to the item on the same transaction line
- Custom menus: Create custom menus to replace native ones and add additional workflows and functionality
- Codeless mobile customizations: Create customized WMS screens that meet the needs of your on-the-floor warehouse tasks easily, right from your mobile device
- Mobile app: Increase productivity and accuracy by using the mobile app for receiving, picking and cycle counting; move between the NetSuite WMS app and other NetSuite mobile apps on the same device
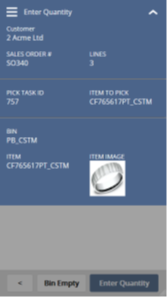
Increase labor productivity and reduce handling time with the mobile app.
2. Guided Inventory Receiving and Putaway
Once you have set up your warehouse layout, your next step is to optimize receiving and putaway. This is where users get recommended bin locations using putaway rules. This functionality includes the following features:
- Initial load of bin inventory: Automatically distribute inventory into bins by CSV import
- Inbound reversal: Reverse received lines on purchase orders, including multiple lines across different purchase orders
- Auto-populate lot expiry date: During receiving, have the system automatically populate the expiry date based on shelf life
- Stage location transfers: Easily move items between staging locations
- Inbound shipment management integration: Receive items using a mobile device and automatically update the associated order and inbound shipment transactions
- Composite barcodes: Utilize GS1 and HIBC barcodes to facilitate the inbound, inventory and outbound processing
3. Optimized Pick, Pack and Ship
The final step is to optimize your organization’s pick, pack and ship processes. This is where you’ll establish rules to streamline your picking process and task assignment. You’ll be able to do the following:
- Strategy definition: Define pick and putaway strategies based on several criteria
- Auto print item labels on receipt: Define labels and have them automatically generated during the receiving process
- Hide expired lots: Optionally hide expired lots during the picking process
- Multi-order picking: Pick items across multiple sales orders in a single session
- Multi-order packing: Pack items across multiple sales orders in a single session
- Pick by order type: Define order types to group orders during picking
- Cross-docking: Direct users to pick inventory from an inbound staged location
- Restrict order changes after picking: After an order line is processed, prevent changes to the line below the picked quantity
- Pick reversal: Quickly reverse a picked transaction line
- Staging picked orders: Stage orders after picking to a specified location
- Fast processing: Support for up to 10,000 order lines per day per picking location
- Wave release process: Create waves of orders based on specific filter criteria which can be released to the warehouse floor for picking and shipping
Role-based dashboards give users a real-time overview of warehouse operations. Pre-built KPIs, key metrics, reminders and shortcuts eliminate the time-consuming task of pulling reports manually.
Key Benefits
To recap, NetSuite’s Warehouse Management System helps you:
- Increase labor productivity
- Improve order fill rates and fulfillment accuracy
- Reduce handling time
- Improve operational efficiency with the mobile app
- Optimize space utilization
- Real-time traceability of inventory movements and transactions
Need Help?
If you’d like to improve your order fill rates and fulfillment accuracy, contact us online or call 410.685.5512 to see a system like this in action.